Hello friends if you are looking for Shop Floor Control SAP PP | Shop Floor Control in Production Planning | Shop Floor Control Configuration in SAP Production Planning | Shop Floor Control Configuration Step by Step in SAP PP | Shop Floor Control Configuration in SAP PP with Notes then you will get all information here
Shop Floor Control – Master Data
In SAP PP (Production Planning), shop floor control refers to the process of managing and monitoring production activities on the shop floor to ensure efficient utilization of resources, adherence to schedules, and timely completion of production orders. Shop floor control plays a crucial role in coordinating and optimizing manufacturing operations, enabling organizations to achieve their production goals effectively. Here’s an overview of shop floor control in SAP PP:
- Production Order Execution: Shop floor control involves the execution of production orders generated in SAP PP. Production orders contain detailed instructions for manufacturing a specific quantity of a product, including the list of materials, routing operations, work center assignments, and scheduling information.
- Resource Allocation: Shop floor control allocates resources such as labor, machines, tools, and materials to production orders based on priority, availability, and capacity constraints. It ensures that the right resources are assigned to the right tasks at the right time to maximize efficiency and productivity.
- Work Center Management: Work centers, which represent physical or logical manufacturing facilities, play a central role in shop floor control. Shop floor control monitors and manages work center activities, including scheduling, capacity planning, production progress tracking, and downtime management.
- Real-Time Monitoring: Shop floor control provides real-time visibility into production activities, allowing supervisors and planners to monitor progress, identify bottlenecks, and take corrective actions as needed. It enables proactive decision-making to ensure smooth production operations and minimize disruptions.
- Production Reporting: Shop floor control collects and records production data such as quantities produced, labor hours worked, machine downtime, and material consumption. This data is used for performance analysis, cost accounting, and continuous improvement initiatives.
- Quality Management: Quality control and assurance are integral parts of shop floor control. It includes monitoring product quality during production, conducting inspections and tests, documenting non-conformances, and implementing corrective and preventive actions to maintain product quality standards.
- Integration with Other Modules: Shop floor control integrates with other SAP modules such as Materials Management (MM), Sales and Distribution (SD), and Quality Management (QM) to ensure seamless coordination across different business functions. It facilitates material procurement, order fulfillment, inventory management, and quality assurance processes.
- Shop Floor Data Collection (SFDC): SAP PP supports shop floor data collection (SFDC) functionality, allowing users to record production data directly from the shop floor using various input devices such as barcode scanners, RFID readers, and touchscreens. SFDC streamlines data capture, reduces manual errors, and improves data accuracy and timeliness.
Define Order types
Transaction Code: OPJH
Menu Path: Production → Master Data → Order → Define Order Types
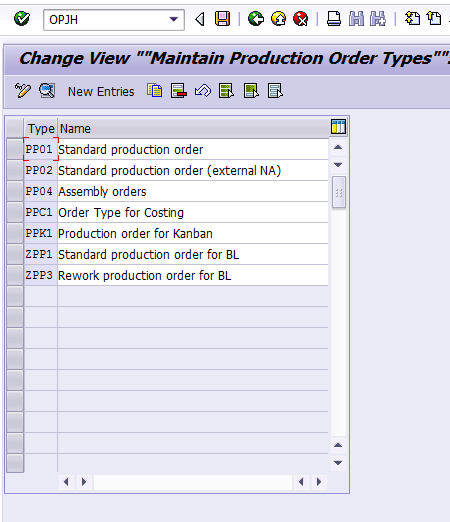
ZPP1 Order type is for Normal production
ZPP3 Order type is for Rework orders


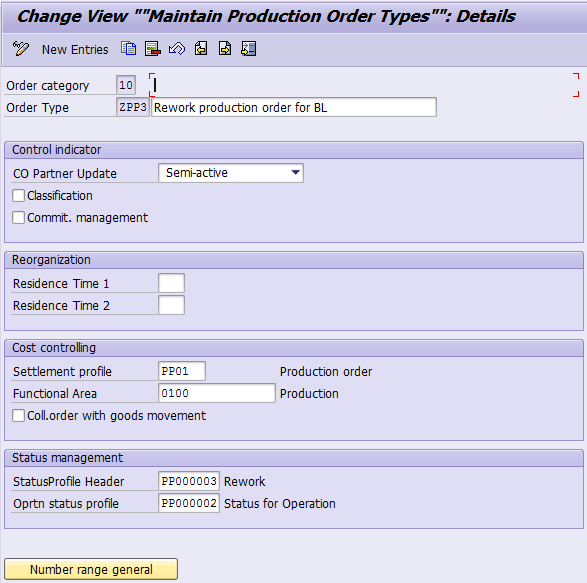
Configuration Details:
In this step one defines order types. An order type contains control information that
need for managing orders. One has to assign every order to an order type.
Status management: An order can go through several processing statuses. Among
other things, the status controls which business transactions are allowed in the
order.
Define Order Type Dependent Parameters
Transaction Code: OPL8
Menu Path: Production → Master Data Order Define Order Type Dependent
Parameters

Details Overview: Planning Tab – Order Type: ZPP1
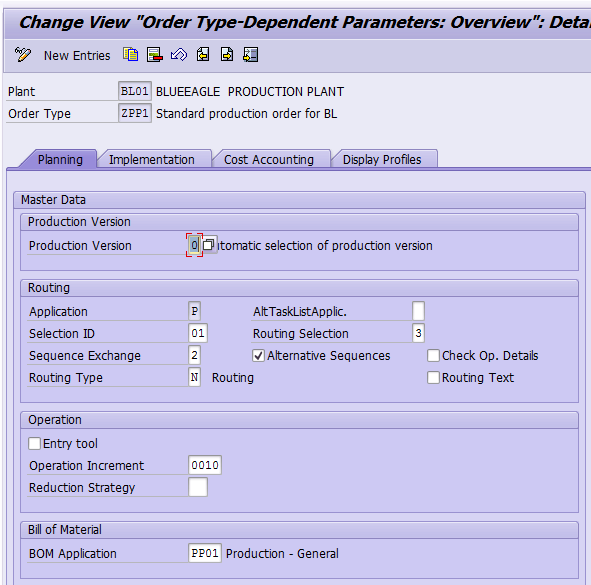
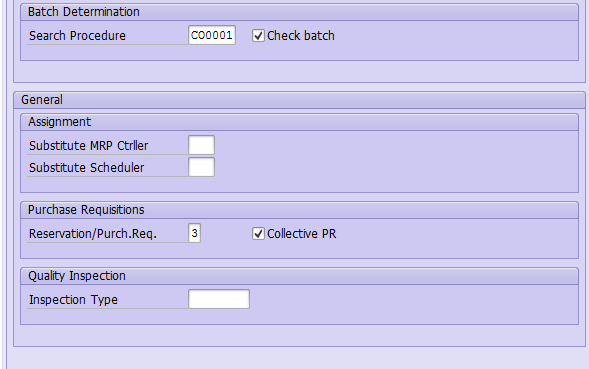
Details Overview: Implementation Tab – Order Type: ZPP1

Implementation tab:
Status change documents
Here, one defines whether one want change documents to be written if a status
change occurs. One also define the level at which the change documents are to be
written. Status change documents can also be defined independently of each other,
at each of these four levels.
Shop Floor Information System
One can specify, for example, whether order data is to be stored in the Shop Floor
Information System. One can carry out reports using this system, for example, for
materials, orders and work centers.
Documentation of goods movements
Here, one can specify that goods movements are to be documented with reference
to an order. Then one can display goods movements, for example, using the order
information system.
Details Overview: Controlling Tab – Order Type: ZPP1
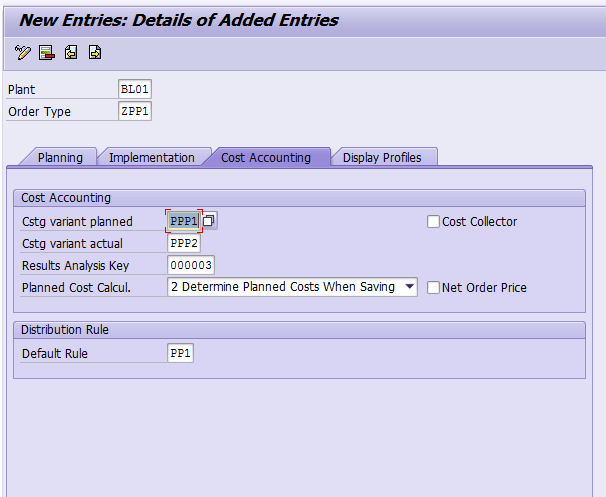
Controlling tab:
Controlling: Here, one defines the parameters relevant to controlling, such as, for
example, costing variants for planned and actual costs and a results analysis key.
Distribution rule: Default (distribution) rule defines an automatically generated
distribution rule for CO settlement.
Details Overview: Display Profiles – Order Type: ZPP1
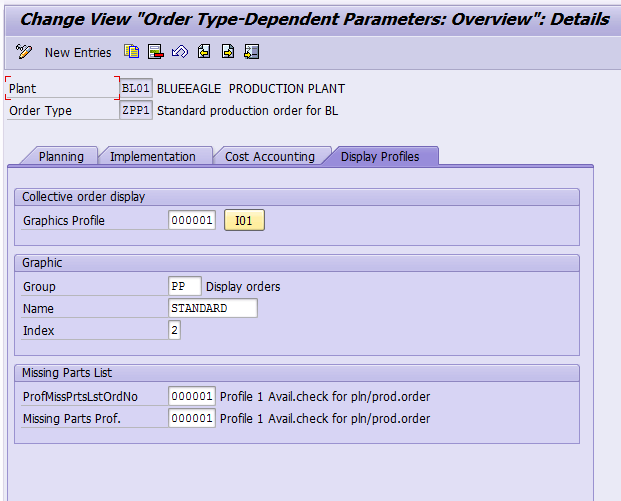
Display Profile tab:
Display profiles Graphic: Here, one defines parameters for displaying graphics of
operations and sequences in the order.
Missing parts list: defines how the missing parts list is to be displayed.
Details Overview: Planning Tab – Order Type: ZPP3


Planning tab:
Master data
Here, one defines the data that influences master data selection or order master data
maintenance:
The task list application is predefined as ‘N’. However, one can also specify an additional task
list application.
Routing
The routing selection ID defines, for example, the ranking order for routing selection.
Routing selection defines whether routings are to be selected and if so, how (manually or
automatically) and whether reference operation sets can also be selected.
The task list type defines which routing type is permitted for production orders.
Operation
Operation detail check defines whether operation detail screens are to be checked when the
operations are transferred to the order.
Routing text defines that the text from the routing header is copied into the order.
BOM application defines how the BOM alternatives are to be automatically selected.
Search procedure defines how batch determination is to take place
General
Substitute MRP controller/substitute production scheduler are proposed when one create
production orders if an MRP controller or production scheduler are not specified in the
material master, or if there is no reference to material.
Reservation/Purchase Req. specifies whether certain order objects (operation, components)
are relevant to MRP.
Collective purchase requisition, Enables collective purchase requisition per order for
externally processed operations or non-stock items.
Inspection type defines how a quality inspection is to be carried out.
Details Overview: Implementation Tab – Order Type: ZPP3

Implementation tab:
Status change documents
Here, one defines whether one want change documents to be written if a status
change occurs. One also define the level at which the change documents are to
be written. Status change documents can also be defined independently of each
other, at each of these four levels.
Shop Floor Information System
One can specify, for example, whether order data is to be stored in the Shop
Floor Information System. One can carry out reports using this system, for
example, for materials, orders and work centers.
Documentation of goods movements
Here, one can specify that goods movements are to be documented with
reference to an order. Then one can display goods movements, for example,
using the order information system.
Details Overview: Controlling Tab – Order Type: ZPP3

Details Overview: Display Profiles Tab: ZPP3
