Hello friends if you are looking for SAP MM Support Project Question and answers so here you will get all the latest Answers related to the same.
We have collected the information for you so that you can use that information to solve your incidents into the project which you are working on.
1) The following is set up for workflow:
- Workflow organization Structure with 2 positions is created and assigned a person to
both positions - Assign tasks to agent
TS 00007986 Requisition release – TO JOBS
TS 00008014 Purchase requisition release refused – GENERAL
TS 00008018 Requisition released – GENERAL
TS 00008348 Requisition release reset – GENERAL
WS 00000038 Workflow for purchase requisition release – TO JOBS - Activate event linkage
WS 00000038 Workflow for purchase requisition release
WE BUS2009 RELEASESTEPCREATE Purchase requisition Release step create is
activated - Activated release codes for workflow
[1= Role resolution with group, code, and plant (T16FW)] - Assigned release codes to agent (JOBS created in 1)
The following error appears
“Work item 60772: Linkage to object BUS2009 event REJECTED cannot be written “.
Ans:
Use transaction SWE2. Make sure “object BUS2009 event REJECTED” is enabled
2) We could create two Purchase Orders for full amount & quantity out of one Purchase
Requisition. two goods receipts and invoice receipts on their respective POs. How can We
avoid this kind of double transactions?
Ans:
For PO ‘s:
Define buyers’ functional authorizations in the customizing for purchasing, there you can
unmark PO w/o reference allowed. Buyer’s functional authorization, say ‘abc’ can be created
using transaction code OMET.
Assign this ‘abc’ to a particular user by using parameter ID “EFB” (trans su52).
For GR and IR:
Make the warning message as an error in customizing of messages under Inventory
Management or Invoice
Verification, respectively.
For IR:
Mark the indicator in the vendor master for checking of double invoices.
3) Is there a transaction or Report available to see the scrapped quantity of a particular
material where goods issue is done using movement type 551?
Ans:
If you want to manage the inventory of Scrap, create another material ID for scrap and receive
as byproduct. When you issue goods against Movement type 551, the material is removed from
inventory by writing it off the books.
4) We want to run multi-plant planning for 3 plants A, B and C , where the requirements
of plant A and B are transferred to Plant C. Plant C is expected to consolidate the
requirement and convert these requirements into requisitions and then into POs. When we
do a planning at Plant C, we are unable to see the requirements for plant A and plant B.
We are using the special procurement key 40 for all the materials being planned. Can we
do multi plant planning at plant level as well as Material level?
Ans:
The special procurement key is defined for the Planning plant and does not contain supplying
plant. This key may be copied to create new key. Then enter the supplying plant in it. Use this
key in material master. Now all the requirements of plant A and B will be called in planning
plant C.
5) We are doing goods receipt with PO . How can we find whether there is any USER
EXIT available which is triggered before the document is saved?
Ans:
The User exit in your case could be MB_CF001 and use transaction SMOD to look for user
exits
6) In MM pricing schema, there are a list of selection from A to M and 1 to 8. How can we
make use of the condition sub-total field?
Ans:
Subtotal field on Pricing schema are useful in number of cases.
# For Ex: 1 is Carry over value to KOMP-KZWI1.
# 7 is used for deciding on the basis for which to calculate Rebate subsequent settlement.
# S is used for the final net inclusive, cash discount, rebates and any other conditions including
statistical
# For reporting in LIS
# Used in the layout for printing.
7) There are some complaints that though the data is correct in User Info (USR03) ,
Purchase order is being printed with wrong information . For Example: telephone
Number. Where can I find correct Purchase group Information?
Ans:
Purchase group information is in table T024.
8) What are the tables generally used for MM Queries?
Some tables are listed below . However a host of others can be seen using Technical help after
activating the query.
- Purchasing Tables
- Purchase Order – CEBAN
- Purchase Requisitions – EKPO
- Material Master
- Description MAKT
- Material master MARA
- Material master – segment C MARC
- Material to BOM Link MAST
- Material Valuation MBEW
- BOM Table
- BOM Header STKO
- BOM item STPO
- BOM Sub-item STPU
- Purchase Group information – T024
- MRP Header MDKP
- MRP Table MDTB
9) What are the typical transaction codes for IM & PO?
Ans:
Transaction codes can be checked using menu path System->Service->Status.
IM transaction codes start with MBxx.
PO transaction codes start with Mexx.
10) During a good issue for a inventory product (HIBE), we assign by the automatic
account assignment a GL account in relation to the valuation class of the product.
However we would like to change this GL account automatically depending of the cost
center requested the product for consumption. How can we do it?
Ans:
Try OKB9 where you can find the cost center account assignment table. However this GL
account becomes defaulted for all the products used by the cost center. Note that GBB/VBR
process key governs the credit posting for cost center issues in Automatic Account Assignment
(AAA).
If you want change Account assignment for exception materials , try the following options:
1.For all exception materials define a new valuation class and setup all inventory posting
accounts for this exception valuation class. Here the AAA automatically picks up the G/L a/c.
2.In the inventory screen allow the user to enter G/L a/c manually . Configure the IMG in
inventory so that user account overrides the AAA determined account
3.Define a new movement type by copying 201 to say 901. Then in Valuation IMG define a
transaction key for 901 under account grouping for movement. types. Define G/L accounts for
this new transaction key. For exception issues users have to use this new movement type.
11) We have specified in MRP for requisitions to be created. The document type of the
requisitions created is always the type NB. How can we change the document type created?
Ans:
Refer transaction ‘OMH5’. Define the document type required that you want in ME51.
12) We have created a workflow for the purchase requisition approval process . When the
event (BUS2009, RELEASESTEPCREATED) is triggered to kick off WF, the following
error message is appearing
Work item XXXXXX: Linkage to object BUS2009 event REJECTED cannot be written.
Diagnosis: The instance linkage between the required event and the specified work item
cannot be entered in the type linkage table of the event manager. The reason is either a
database error or an error when generating internal linkage numbers. What to do: Check
the number range object ‘SWE_EVTID’ How can this be fixed?
Ans:
- Must update the number range for events object SWE_EVTID with transaction SNRO.
Ex: SWE_EVTID: 01 000000000001 999999999999. - SWE2, double click on BUS2009 entries, check GLOBAL field, ENABLE field will be
updated - Error when executing the Workflow. Transaction code SWLE not defined. Apply OSS note
43986 to fix.
13) How can we make a Taxcode as default on purchase order item detail screen?
Ans 1:
Use condition type NAVS with access sequence 0003 to default the taxcode in the purchase
order item using conditions.
Ans 2:
Go to IMG.
Materials Management -> Purchasing -> Purchase Order -> Define screen layout at document
level.
Search for the transaction ME21N. Double click on ME21N. Then search for TaxCode (in
GR/IR Control). It is advisable to configure also the info record. The tax code should be a
required entry, and whatever you specify here will be the default value in the Purchase order.
Materials Management -> Purchasing -> Purchasing info record -> define screen layout.
When you get here you search for the transaction ME12, double click here; search for Input
VAT indicator
14) We have defined EA (each) as 0 decimal place in configuration. But transaction ME2L
shows this field with three decimal places. How can I change to actual number of decimal
places?
Ans:
The quantity (MENGE) in that report must have been set for 3 decimal places. Table EKPO may
have to be corrected accordingly.
15) We have created a new movement type and assigned to a schedule line. When goods
issue is posted, message – movement type zzz is not allowed for customer goods movement?
Why?
Ans:
Use transaction code OMJJ and check the “Allowed Transactions” for customizing movement
types.
Lock a field in material master from change
16)You have a requirement to protect the field MARC-SERNP ‘Serial number profile’,
found within the material master data ‘Sales General/Plant’ and ‘Plant data / stor.2’ tabs,
from being changed by all but two employees.
How can you restrict change access to the material master data views entirely through
authorisation settings or any other good method to control this?
Answer:
A couple of options are:
- Create a transaction variant with that field as display only. Assign variant to a custom z-tcode
and distribute (cons are that most users use the custom z-tcode). - Work with a developer to use the enhancement framework to restrict that field to display only
unless users have additional auth (e.g. new auth object or re-used existing).
17) How to edit the description name of a storage location?
It is very simple, go to OX09 and straight away you can change the Storage location name. Only
thing is that you should have access to change it and in view mode it is greyed out and not
possible to change. If you want to change the address of S.Loc, select the desired S.Loc double
click on address folder in left side, it allow you to maintain the address too.
18) Is it possible to maintain the same material master with same code in all plants in a
company. Our client is using same materials in all their four plants?
Material numbers are always maintained at Company code level. If you look at the Material
master data, some data is maintained at Company code level, some at Plant level and some at
Storage location level. If you have all the 4 plants attached to one company code, they should
have the same material number. What you need to do is to extend the material to all the 4 plants
if thats your requirement. Also, if you have your valuation area as your Plant, then you have the
flexibility to maintain Plant specific pricing for the same material.
You can use MM01 T code to copy material from old plant to new plant. But check for the
required details in your new plant and make changes accordingly.
19) Where we do the configuration for the cost centre allocation, because whenever we GR
a material, accounting document is created for that particular material. How that
particular material go in to the particular accounting (G/L account)
In Tcode: OBYC — Automatic Postings.
for Inventory Posting Trns Key is: BSX
for Off setting entries like Goods issue, initial stock……Trans Key is : GBB
Based on the Movement types, Valuation class it will be assigned to a G/L account.
You can refer the configuration in Tcode: OBYC
20) Could any one can explain complete configuration of pricing procedure & application.
The Basic thing is Condition Technique. In which there are
- Access Sequence 2. Condition Record 3. Condition Type 4. Condition Table.
A Access Sequence access a Condition Record of a Condition Type in a Condition Table is
a Condition Technique.This is a simple logic
Here the Condition Type is very important like PB00, PBXX,RA01 etc.
In the background every Condition Type has its own defition means the purpose of the
Condition Type like, is it for Pricing or Percentage, Quntity base, Accrual Feilds etc is to be
defined to work this functions. Normally we use the existing ones without any risk. But some
cases, we have to Create a New Condition Types as per the organisation requirement.
The Pricing Schema is useful to minimise condition types while mention prices for Vendor on
the basis of Pricing Schema which we defined according to organisation requirement.
The Pricing Schema means the calculations procedure of Condition Type.
Ex. RA01 – Discoount % is caclulated on PB00 – Gross Price means
RA01 is based on PB00 like that we have to define in the Pricing Schema
which makes easy to use in real time.
Here PB00 has the Access Sequence – 0002.
But RA01 does not have the Access Sequence.Why because it is a dependent on PB00. But both
are Condition Types.
In the system, by default some standard Scheme will be there at Vendor Schema Group in the
Vendor Master Screen means the standard one is assigned which is very lengthy which may
fullfil our requirement. But some cases which may not fullfil our requirement, in such we have
to define.
For the configuration, I may not able to explain properly through here but will give some idea.
Configuration: SPRO – IMG – Material Management – Purchasing – Conditions – Define Price
Deternmination Process: - Define Access Sequence
- Define Condition Type
- Defince Calculation Schema:- Here you have to define the Schema – Define Schema group
- Define Schema Group vendor
- Define Pricing Schema group
- Schema group for Purchase Organisation
- Assign Schema group to Purchase Organisation – Define Schema determination
1.define calculation schema for Standard purchase organisation
After completion of the Schema Group, we have to assign it to Vendors.
Then whenever we use any transaction with this Vendor, the concerned Schema will work as
configured by us. The Pricing in MM is vast because each Condition have its own importance
and each Access Sequence have its own importance. So you need not bother about this. First
you learn how to define the Calculation Schema through the above.
21) What are the possible reasons for taking long run time for MB5B?

22) How to stop the cancellation of Goods Receipt Material Document before cancelling
Invoice Receipt Document?





23) How to stop the Purchase Order creation from expired Contract in SAP MM?

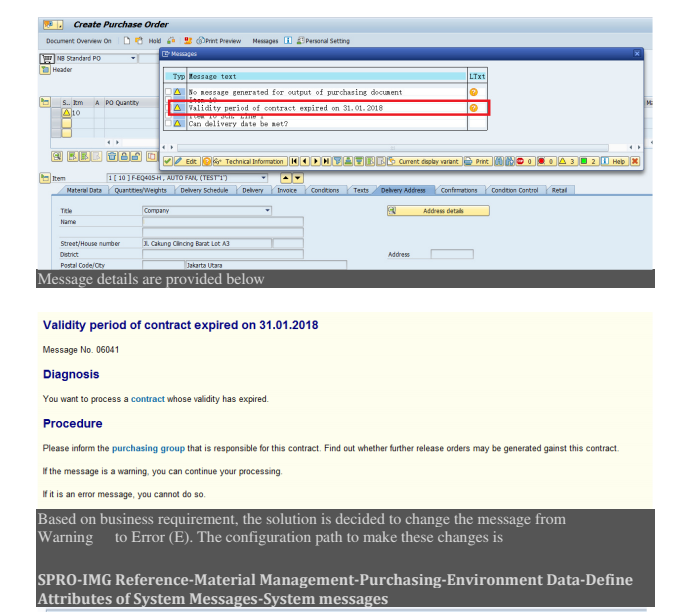
24) Conversion of IDoc Status
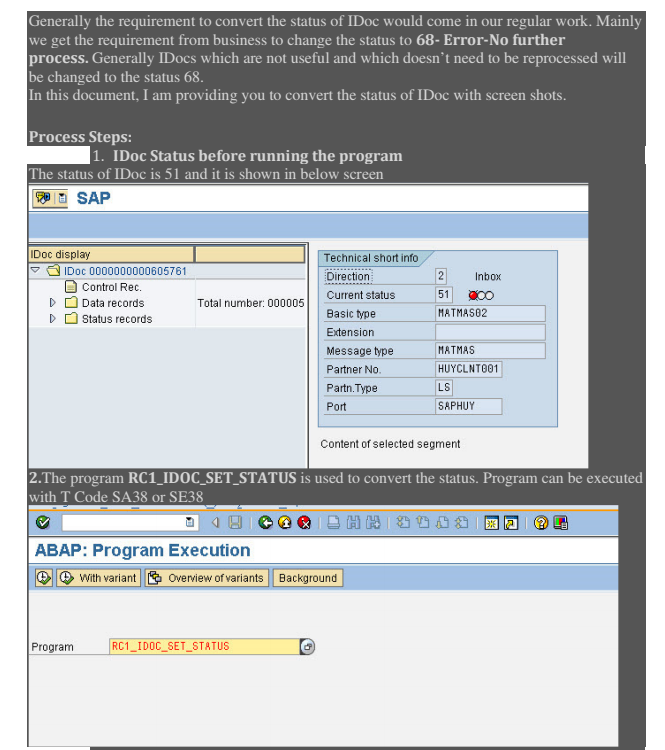
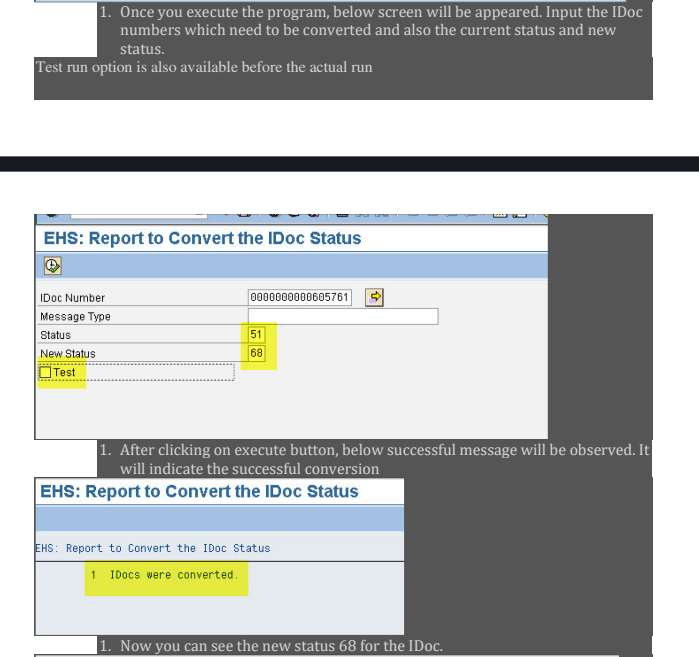

25) How to get the Accounting document against Material document in SAP?
Requirement: Business has the requirement to get the list of Accounting documents against
respective Material document(s). As we aware that whenever a Goods movement happens, a
material document and accounting document will be generated automatically.
Solution:
In this document, I have explained the process of getting Accounting documents from Material
documents with screen shots.
Important Table and Fields which are used in this document
Table – BKPF – Accounting Document Header
Input Screen:
Input Fields – AWTYP– Reference Transaction. As we are giving Material document as input,
reference transaction has to be given as MKPF (This field is an optional. You can pass only
AWKEY to get the output because AWTYP will vary among the transactions)
AWKEY – Reference Key. Reference key has to be given the combination of Material
document+Material document Year ( MBLNR+MJAHR). While givin the material document,
you have to give the total number length (here it is 10)

26) How to block a vendor in SAP?
Vendor can be blocked at different levels in SAP as per the requirement. I have provided few important blocking
functionalities of vendor which will be useful for you.
- Vendor block at Purchase Organization Level:
Transaction Code: MK05
Vendor can be blocked for a specific purchase organization or for all the purchase organizations. Respective
steps are given below. This type of requirement comes from business if they want to stop the procurement
operations from a vendor for specific purchase organization.
Step 1: Initial screen of MK05 will be visible as shown below. Input the Vendor and the purchase
organization.

Step 2: Blocking reason can be given during blocking. And also blocking for given purchase organization or
for all the purchase organizations also can be decided. Respective details are highlighted in below screen.

- Vendor block at Company Code Level:
Transaction Code: FK05
Vendor can be blocked for a specific company code or for all the company codes. Respective steps are given
below.
Step 1: Initial screen of FK05 will be visible as shown below. Input the Vendor and the Company Code.

Step 2: Blocking for given company code or for all the company codes can be decided. Respective fields are
highlighted below.
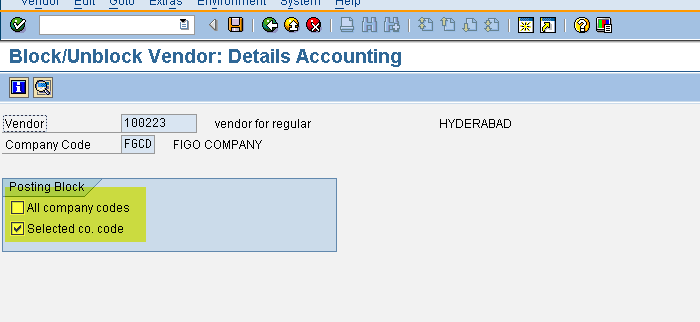
- Vendor block for Material and Vendor :
Transaction Code: ME01
Source list is used to block or fix a vendor for procurement. In this source list blocking of vendor will happen
for the combination of Plant and Material.
Step 1: Enter the material and plant in input screen.

Step 2: Validity period in which period the vendor needs to be blocked has to be given. Blocking flag is
highlighted below

We hope so You will find this information good.