Hello friends if you are looking for SAP Production Planning Notes | SAP Production Planning Step by step Configuration | SAP PP Configuration Step by Step Process | SAP PP Configuration For Beginners then you will get Help Here.
Material Requirements Production Planning
The main function of material requirements Production Planning is to guarantee material
availability, that is, it is used to procure or produce the requirement quantities on time both
for internal purposes and for sales and distribution. This process involves the monitoring of
stocks and, in particular, the automatic creation of procurement proposals for purchasing and
production.
Plant parameters in Production Planning –
SAP MRP is run at plant level or at a group of plant level (called as scope of planning),
thus the MRP configuration is done at Plant level.
The configuration done for SAP MRP at Plant level would also be true for SAP
Consumption Based Planning (SAP CBP) settings.
Overall maintenance of Plant parameters –
Transaction Code: OPPQ
Menu Path: Production → Material Requirements Planning → Plant Parameters Carry out Overall
Maintenance of Plant Parameters
Here we can create or maintain all the plant parameters for MRP.

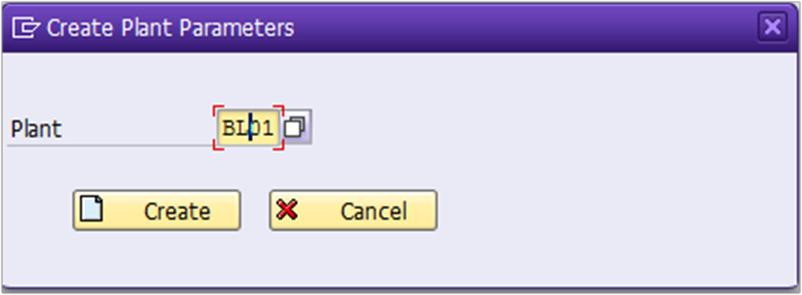
Following are the parameters that need to maintain as a part of SAP MRP Configuration:
a) Number ranges
The number range ID’s are maintained for the following objects:
- the Planned orders
- the reservations,
- the dependent requirements,
- the simulative dependent requirements,
- the purchase requisitions,
- the MRP Lists,
In this section only the number range ID’s are maintained. While the actual number range is
configured, for the number range ID, using a transaction code OMI2 (for the above mentioned
objects created in the planning run). One can also use the transaction code OMI3 for the objects
created manually in the front end.
Every number range interval, created using OMI2 and OM13, has an ID, which can be allocated
to the objects at plant level, i.e., every plant can have a different number range for the objects
mentioned above.
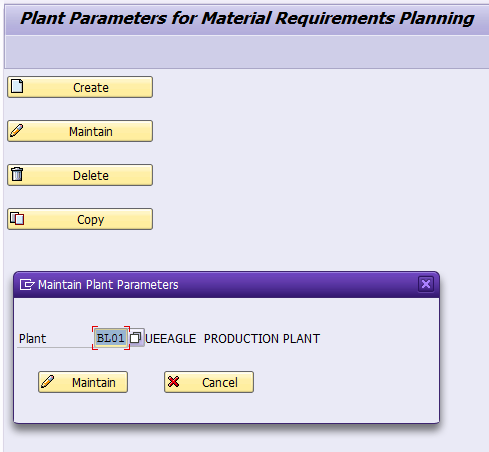



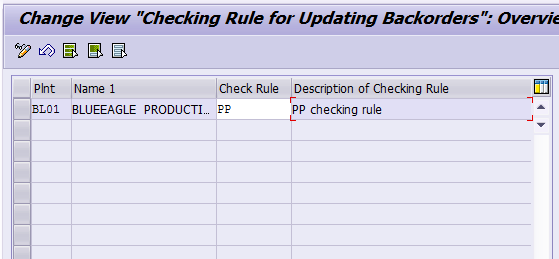
c) MRP Controllers
This is a mandatory configuration. Here you can configure the list of MRP controllers for the
plant. A MRP Controller is a person or a group of people, which is responsible for planning a
material or a given list of materials.
You have to assign the MRP controller to the Material Master MRP 1 View, so as to delegate
the responsibility of the planning and evaluation of planning for that material.



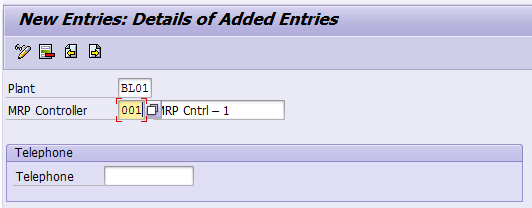



d) Floats
Floats are buffers in the total lead time, that are provided in production/process order or in the
planned orders created manually or during an MRP run. The schedule margin key is used in
the Material Master MRP 2 View. It is used in MRP as well as in production order.
The floats are defined using the scheduling margin key.
Opening period: Number of working days between the date that the order is created and the
planned start date. This time is available for the MRP controller to convert a planned order into
a purchase requisition or a production order.
Float after production: Number of working days between the scheduled finish date and the
order finish date; used as a float in production scheduling.
Float before production: Number of working days between the order start date and the
scheduled start date; used as a float in Production Planning.
Scheduling release period: Number of workdays between the planned start date and the date
for releasing the order. If the order release indicator is set, the production order is released by
a background program that takes all dates into account.


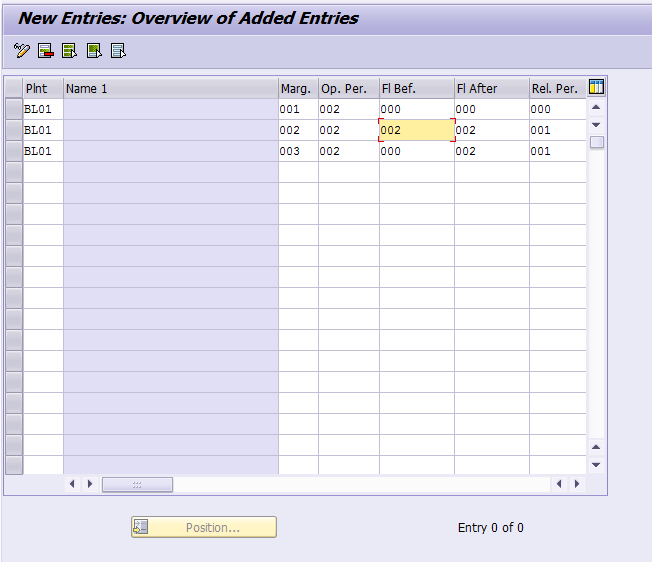
IV) Phantom Item:
If a material is to be identified as the Phantom material, you have to enter a standard special
procurement type – “50” in the material master of the plant where the material is defined a Phantom.
V) Direct production (for Collective order processing)






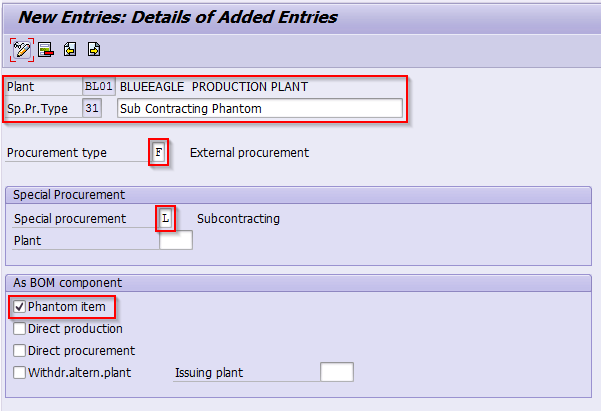

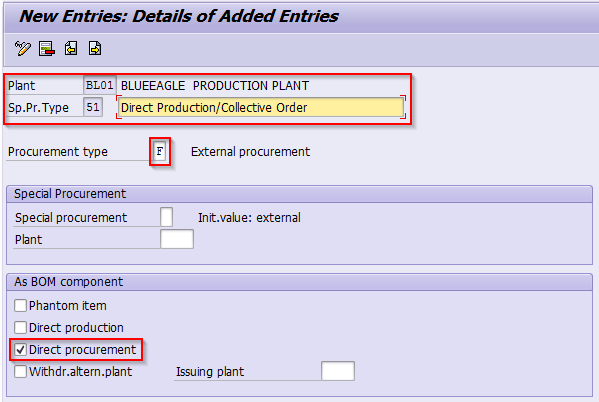
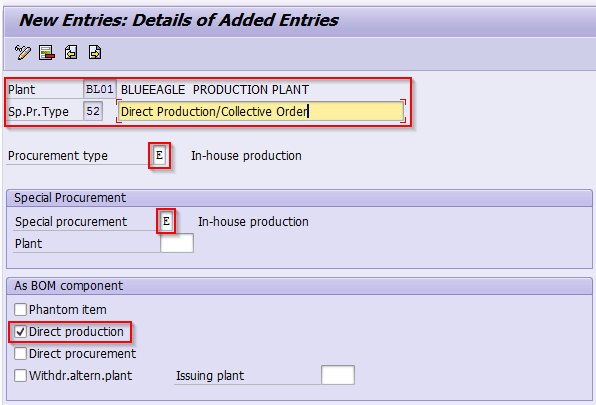
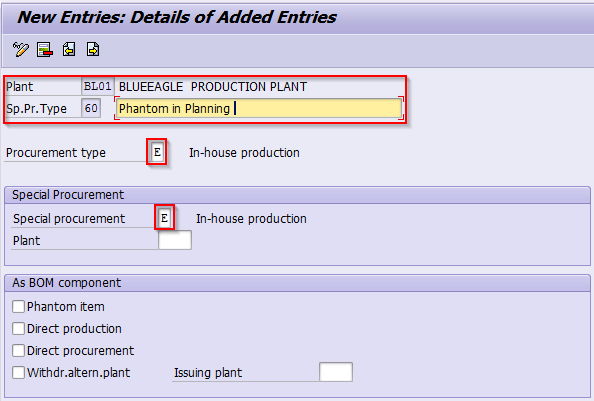
f) Conversion for Planned orders
In this configuration parameter, you can maintain the production order type or the process order
type, which the system should use as default during the planned order conversion. Setting
defaults in the plant parameters configuration allows the system to fix and select the order type
for a plant during the conversion process.
Also for the purchase requisition conversion, you are given an option in the configuration to
define the maximum number of planned orders that can be converted in to Purchase requisition.



MRP parameters in Production Planning
Overall maintenance of MRP groups
Transaction Code: OPPR
The entire configuration that is created as a part of SAP MRP Plant level parameter in the above
steps can be also set for an MRP Group. You can group materials using MRP Groups. Each of
the MRP Group can have its own MRP Parameter set. You can set the MRP group in the
material master MRP 1 View.
MRP Group can be maintained using transaction code OPPR or the transaction path – Logistics
>Production > MRP > MRP Groups >
Advantage of working with MRP Groups:
Working with MRP groups can be convenient for a plant or an organization, since by assigning
the MRP groups to a set of materials, would allow planner to configure these materials (through
MRP Groups) to behave in a certain manner for planning purposes. In other words, all the
materials in the group would then have a unique planning method or unique planning features.
Thus the organization can device multiple MRP groups with their own planning features and
characteristics rather than having one set of planning features set at the plant level. The group
could have its own unique:
Strategy group,
Conversion order types,
Planning horizon,
Planning time fence and roll forward periods,
BOM and task list selection ID’s,
Direct procurement parameters,
Planned order scheduling parameters,
Start number of days allowed in the past
Availability checking groups,
Strategy Groups
The strategy groups can be set for a given MRP group at a given plant. The strategy group
consists of a number of planning strategies assigned in a sequence of priorities. In other words,
the strategy groups, groups together the relevant planning strategies of a material. If you don’t
see the default strategy groups, then we would have to manually maintain the strategy groups
on the materials MRP 3 view. Defaulting the strategy groups is a nice idea when the strategy
groups would remain the same across all the materials which would be assigned with a given
strategy group.
For example:
A material can have the priority 1 strategy as Made-to-Stock (planning strategy 10) and then
priority 2 planning strategy as Made-to-Order (planning strategy 20). Assigning this “strategy
group” for a MRP group in the MRP Group Parameters configuration and then subsequently
assigning the MRP Group to the material master would make the material work on a planning
strategy 10 and planning strategy 20 in a sequence of priority.
The primary strategy for the material is 10 – Made-to-stock while the secondary strategy is 20
– Made-to-order, which means that every time you plan or produce a material or create a sales
order for the material it will always primarily work as a made-to-stock material. Nevertheless,
you can also make to material work as a made-to-order material, by changing the requirement
type – “KE” of the material in the sales order procurement tab, to suit for made-to-order, which
the system would allow since the material’s secondary planning strategy is made-to-order.




Similarly MRP Group 0004 for in- house production without PIR was created.
To Maintain MRP Group,
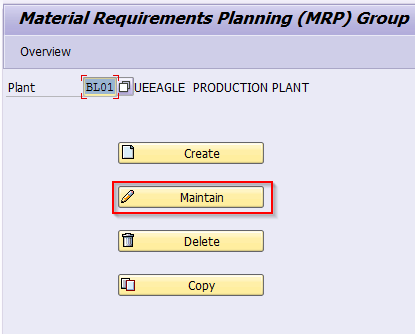
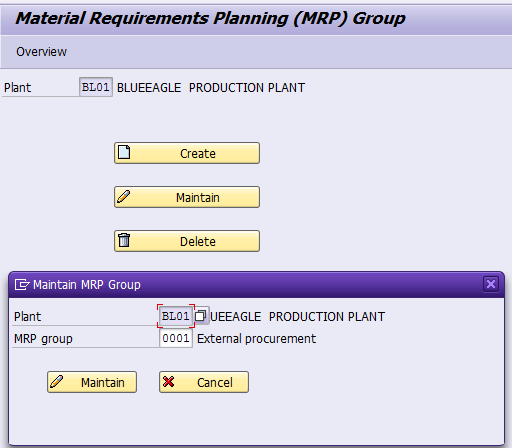


Similarly,
MRP Group Strategy Group
0002 : 10
0003 : 10
0004 : 20
Following MRP groups are defined for Blue Eagle
