Outline Agreement refers to a long-term procurement arrangement between a buyer and a vendor for the supply of goods or services over a specified period. It serves as a framework agreement that establishes terms and conditions, pricing, quantities, and delivery schedules for multiple purchase orders issued under the agreement.
Outline Agreement In SAP MM
“These are short term and long term and long term agreements with the vendor to supply
goods and services under certain conditions”
Vendor selection is an important process in the procurement cycle; vendor can be selected by
quotation process. After getting shortlisted a vendor, an organization enters into an agreement
with that particular vendor to supply certain items with conditions. Typically when the
agreement reached with that particular vendor, a formal contract is signed with the vendor. So
the outline agreement is a long-term purchasing with vendor
The key points to taken care about outline agreement here
An outline agreement is a one-term purchasing agreement with a vendor containing terms and
conditions regarding the material that is to be supplied by the vendor.
The terms of outline agreement are valid up to certain period of time and cover a certain
predefined quantity or value.
Types of Outline Agreements:
- SAP MM supports different types of Outline Agreements, including:
- Contract: A legally binding agreement that specifies fixed terms and conditions, pricing, and quantities for the entire duration of the contract.
- Scheduling Agreement: A flexible agreement that allows for the release of specific quantities at predefined delivery dates within the agreement period.
- Framework Purchase Order: A general agreement that provides a framework for future purchase orders without specifying specific quantities or delivery dates.
Creation and Maintenance:
- Outline Agreements are created and maintained using transaction codes such as ME31K (Create Contract), ME31L (Create Scheduling Agreement), and ME31 (Create Framework Order).
- During creation, users input details such as vendor information, material details, pricing conditions, delivery schedules, and terms of the agreement.
- Maintenance activities include updating agreement data, extending validity periods, changing quantities or pricing conditions, and managing amendments or cancellations.
Key Elements:
- Outline Agreements in SAP MM typically include the following key elements:
- Vendor Information: Details of the vendor supplying the goods or services, including name, address, and contact information.
- Material Information: Description of the goods or services being procured, including material number, description, and unit of measure.
- Pricing Conditions: Pricing terms, including unit prices, discounts, surcharges, and currency.
- Delivery Schedules: Scheduled delivery dates and quantities for the ordered items, allowing for phased delivery over time.
- Terms and Conditions: Contractual terms governing the agreement, such as payment terms, delivery terms, and warranties.
Integration with Procurement Processes:
- Outline Agreements are integrated with other procurement processes in SAP MM, such as Purchase Requisitions (PRs) and Purchase Orders (POs).
- Purchase Requisitions can reference existing Outline Agreements to generate Purchase Orders, ensuring compliance with the terms and conditions specified in the agreement.
- Purchase Orders issued under Outline Agreements inherit the pricing, delivery schedules, and other terms established in the agreement.
Monitoring and Reporting:
- SAP provides tools and reports for monitoring and analyzing Outline Agreements, including transactional reports, analytics dashboards, and Key Performance Indicators (KPIs).
- Users can track agreement usage, monitor delivery performance, analyze spend against contracted terms, and identify opportunities for optimization or renegotiation.
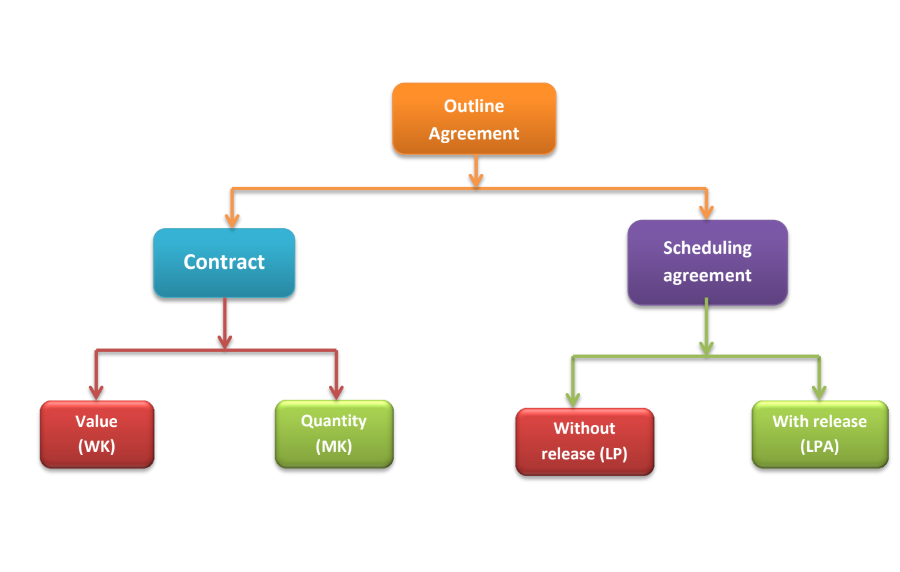
Business scenario
Before – I had one plant Z005 with one purchasing organization i.e. (Z005) and I had a
requirement of materials (464802, 464804) on weekly basis with certain price from vendor
(101046) is supplying me that material from one year.
Now- I have been expanded my business and I have total three plant now i.e. (Z005, Z006,
Z007), with one Purchasing organization (Z005) means I have centralized purchasing
organization,
I want material (464802, 464804) for all three plants and so in this case I am going to
negotiating with vendor, because I have increased volume so I could negotiate with vendor to
reduce the price by saying that I am going to procure material with a quantity 4 times more
than before.
Then the vendor could offer me to make an agreement for a year or six month with better
terms, with better shipment service, better packaging, better price etc. that will be beneficial
for vendor and I too.
So I will create I contract with the vendor for 1 year.
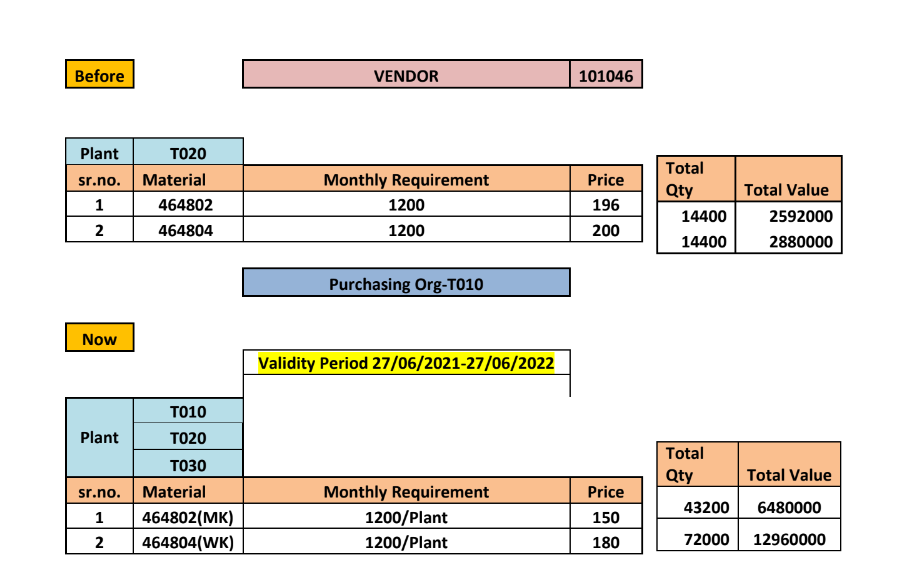
Quantity Contract: The total value of
As per business Requirement I am going to create now a quantity based contract with decided
vendor.
T-CODE: ME31K/32K/33K (Create/Change/Display)
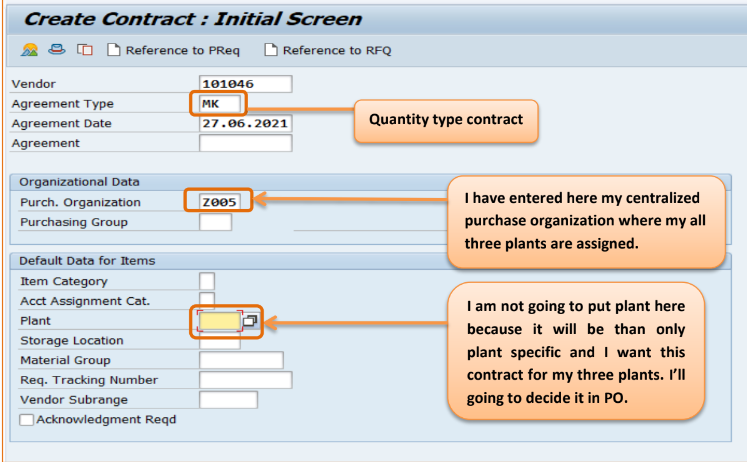
Header data: It includes all contract related data like company code, validity period, we can
also mention approximate value under the contract also we can decide terms of payment
agreed with vendor.
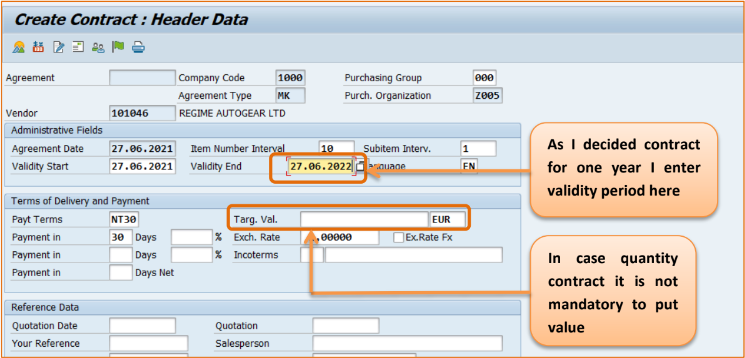
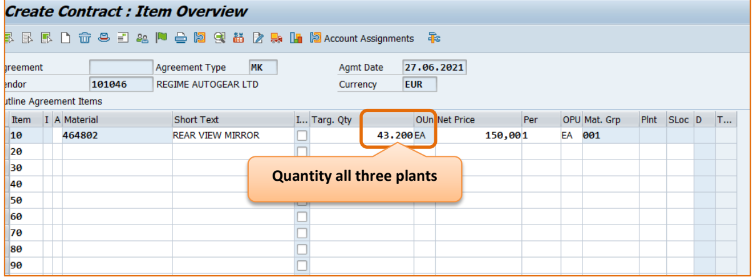
Quantity contract saved
If Purchase order (ME21N) for that material without reference to contract
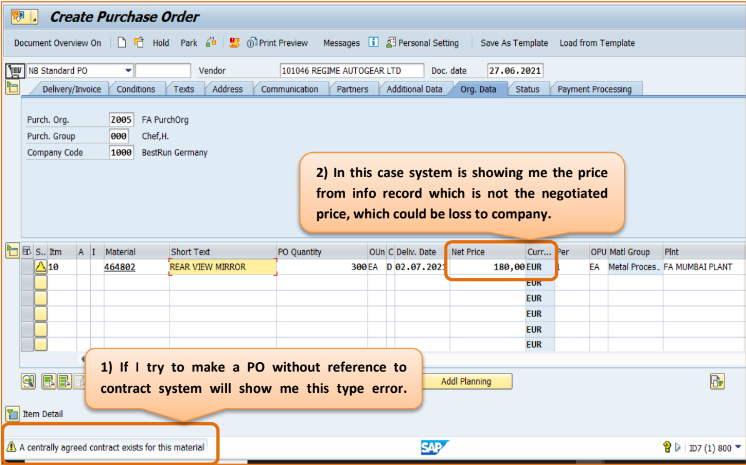
Purchase order (ME21N) with reference to contract

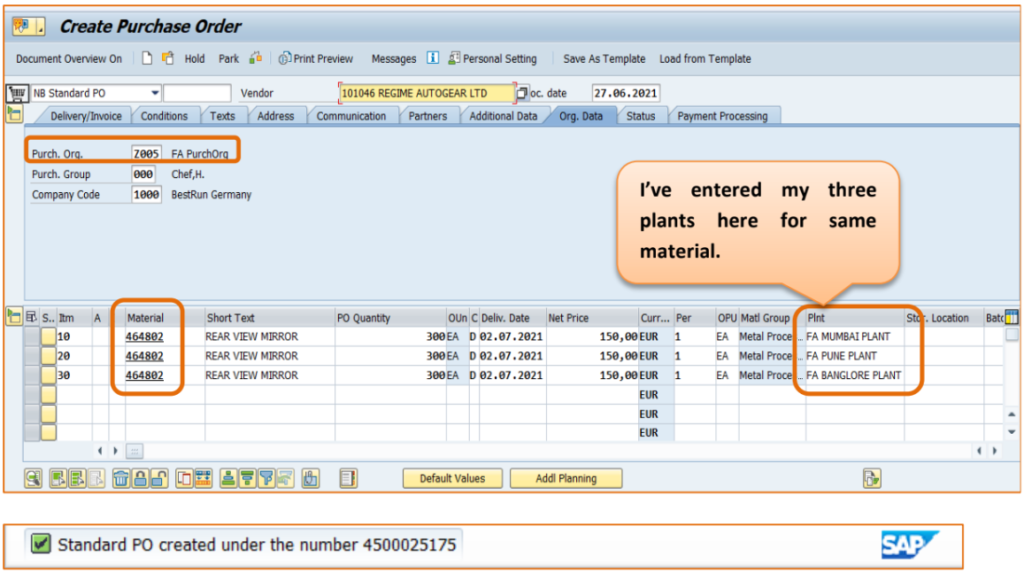
Goods Receipt (MIGO)
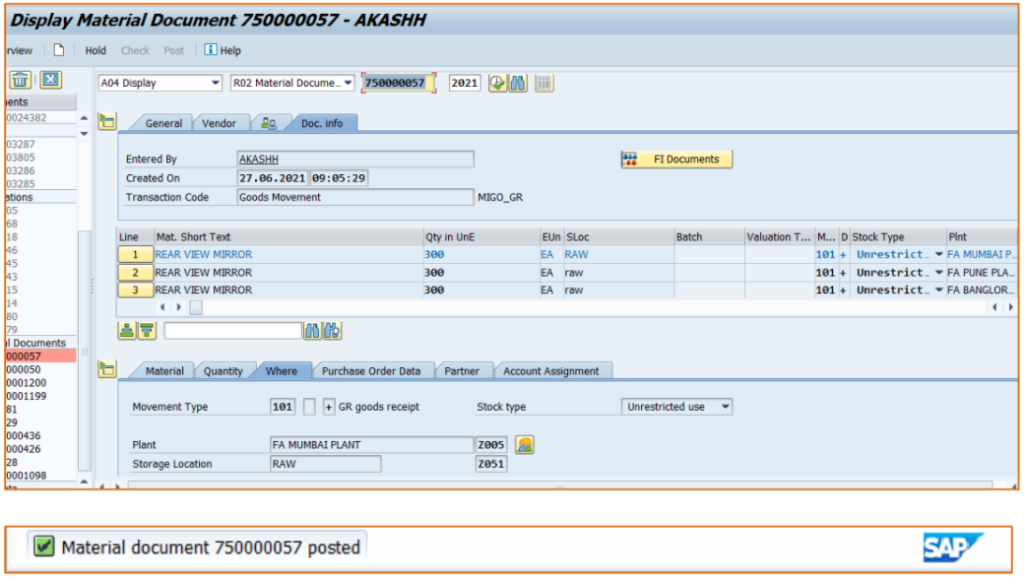
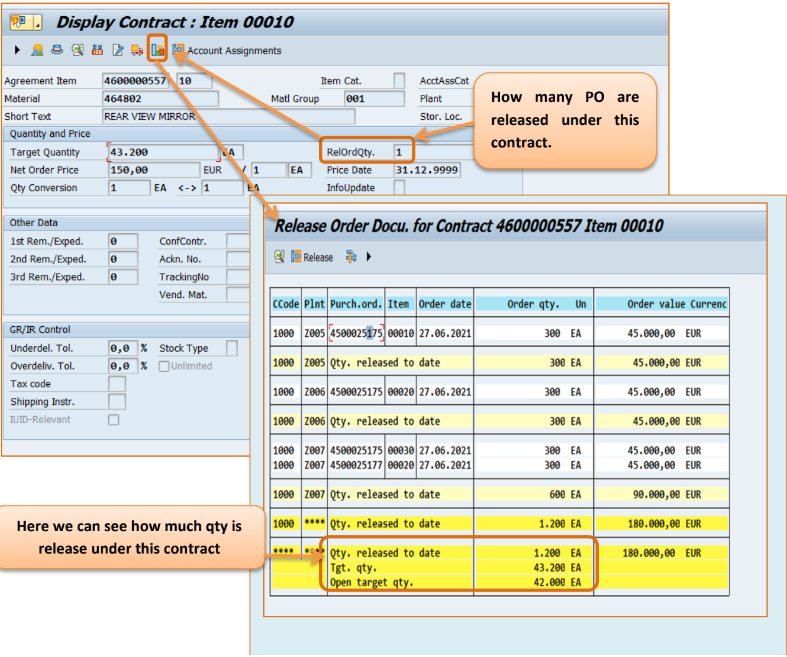
Value contract (WK)
As per business Requirement I am going to create now a Value based contract with decided
vendor.
T-CODE: ME31K/32K/33K (Create/Change/Display
In this case I’ve create contact with reference to the purchase requisition.
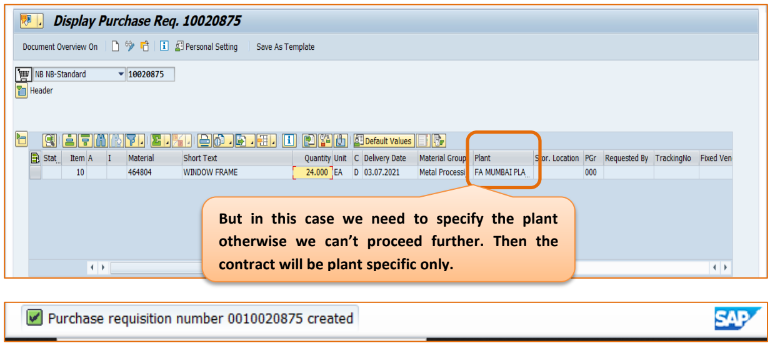
Header data: It includes all contract related data like company code, validity period, we can
also mention approximate value under the contract also we can decide terms of payment
agreed with vendor.
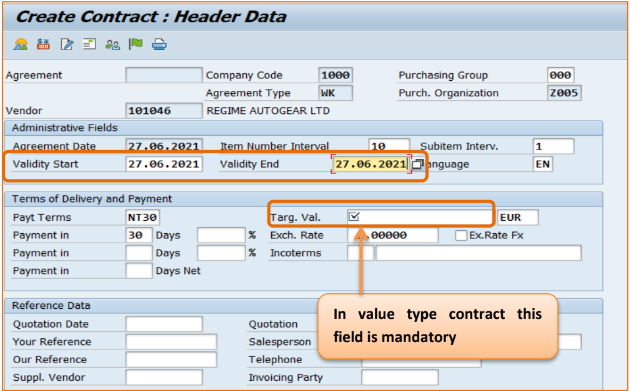
Target quantity and net price must be specifying here.
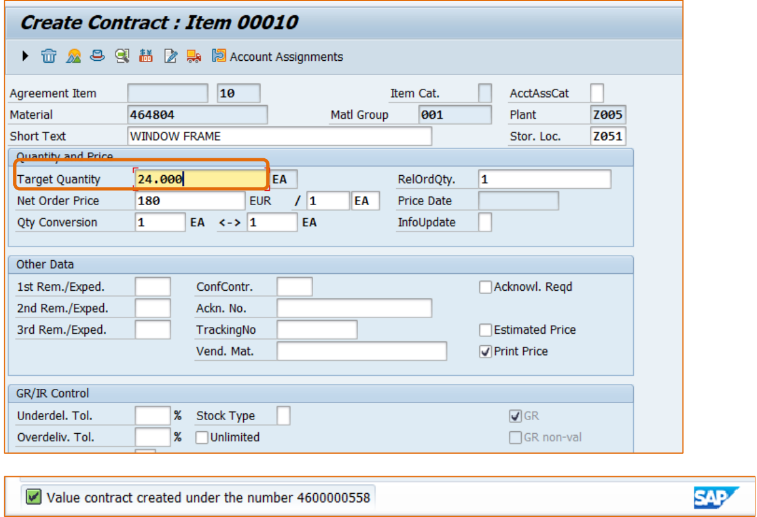
Purchase order with reference to Value and Quantity contract both in the same PO
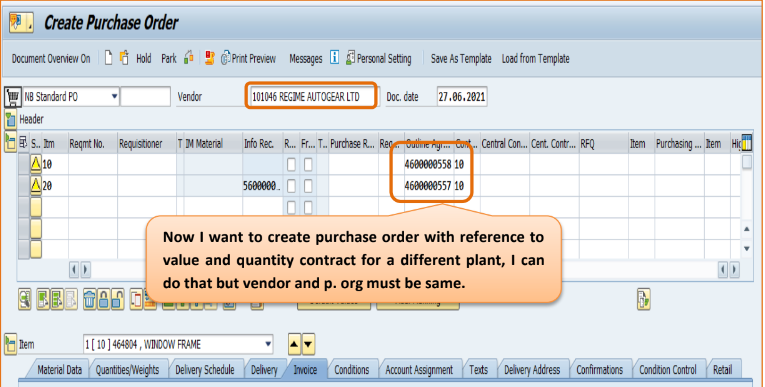
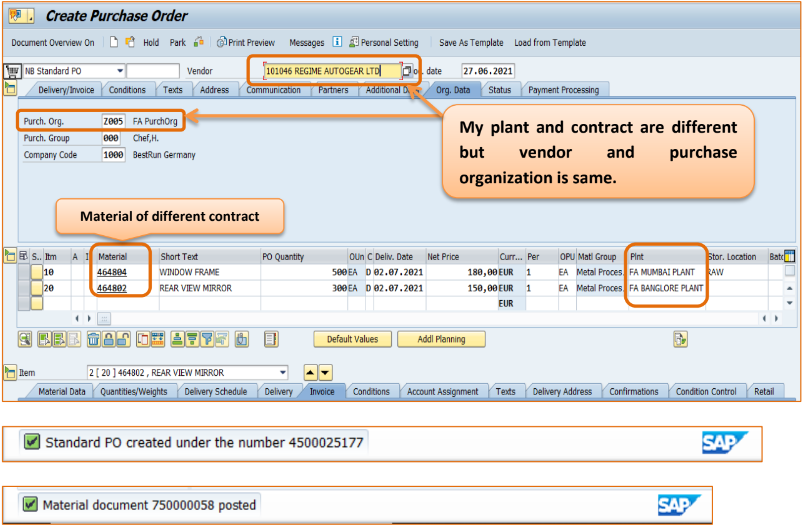
In case of contract we tell the vendor specify the vendor target quantity OR A target value, but
what is I have requirement of material on weekly at particular date of a week in that case with
replacement of contract we can do scheduling agreement with the vendor by specifying the
actual date and quantity.
In this case want material (464810) and I required this material on weekly basis at particular
date.
To avoid any delay in order and save my time from creating PO on weekly basis I will create
scheduling agreement.
STEP 1
Create scheduling Agreement
We have without release (LP) and with release (LPA)
T-CODE: ME31L/32L/33L (create/change/display)
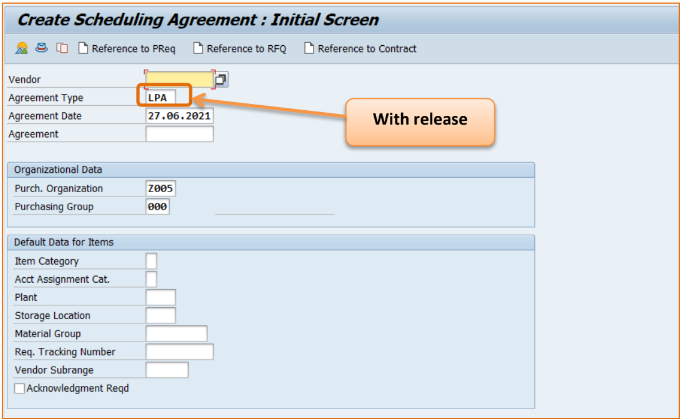
NOTE: For this document I am showing you only with release (LPA) only the difference in
without release we no need to release the document it releases automatically with date.

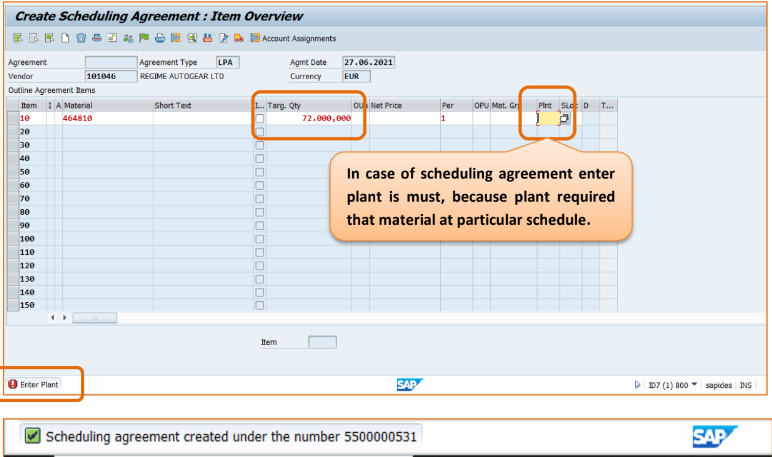
STEP 2: Maintain Scheduling agreement we need to maintain it as per date of delivery and
quantity.
T-CODE: ME38
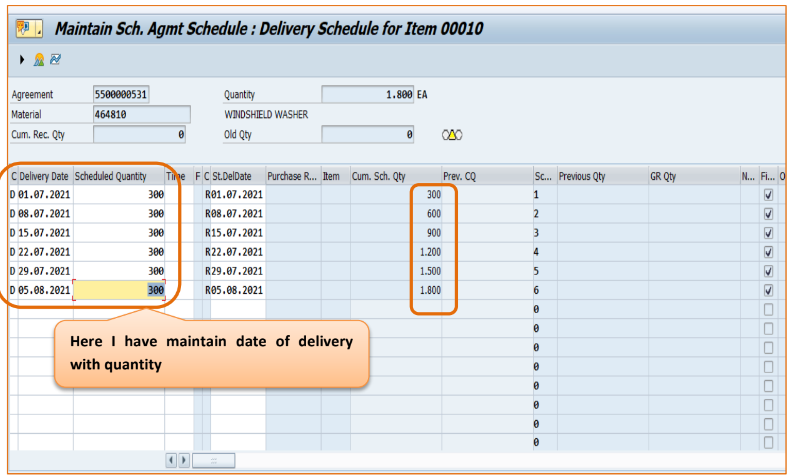
Verify Purchase order ME21N from document overview.
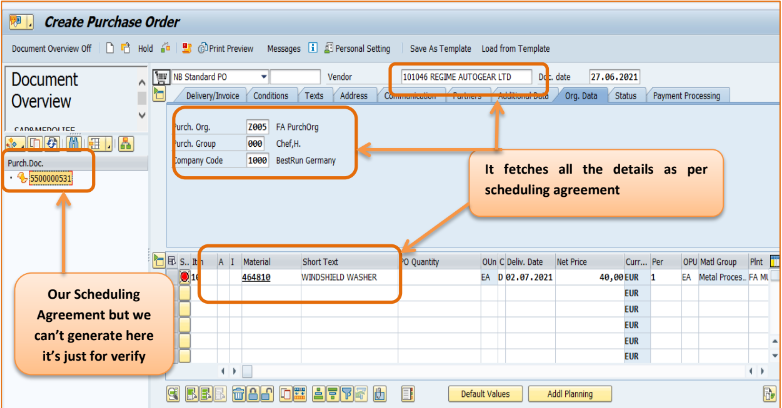
STEP 3
Now I have to release it as per requirement.
T-CODE: ME84
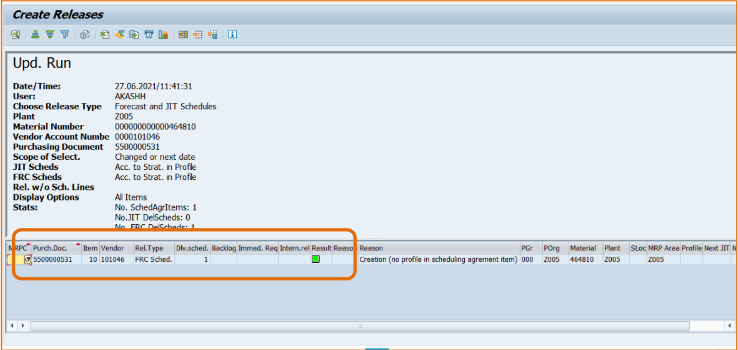