Hello friends if you are looking for Control key in SAP PP | Control key configuration in SAP PP | Control key Configuration Notes in SAP PP | Control key SAP Production Planning Notes | Control key Notes For SAP Production Planning in SAP PP | Availability Check Parameter (OPJK) in SAP PP | Availability Check Parameter (OPJK) Notes in SAP Production Planning then you will get all details here.
In SAP PP (Production Planning), the Control key is a critical element that governs various aspects of production processes and operations. It serves as a defining factor for how a particular production order or operation should be processed and managed within the SAP system. The Control key essentially determines the behavior and characteristics of a production order or operation, influencing factors such as scheduling, capacity requirements, material availability, and costing.
In SAP PP (Production Planning), scheduling is a vital aspect controlled by the Control key. The Control key influences how scheduling parameters are determined for production orders or operations within the system.
T Code: OP00
Control keys are normally pulled in from the work center, if you have entered a default
control key there. Control keys are really important keys in SAP PP.
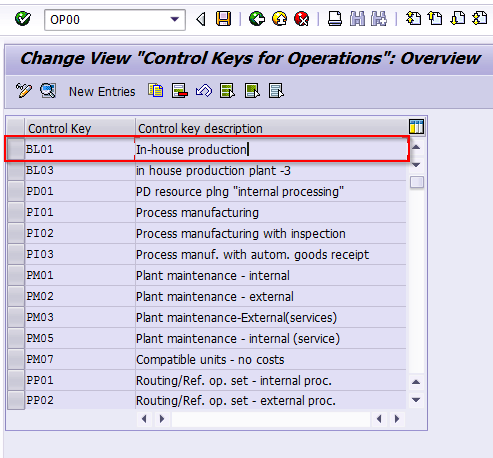
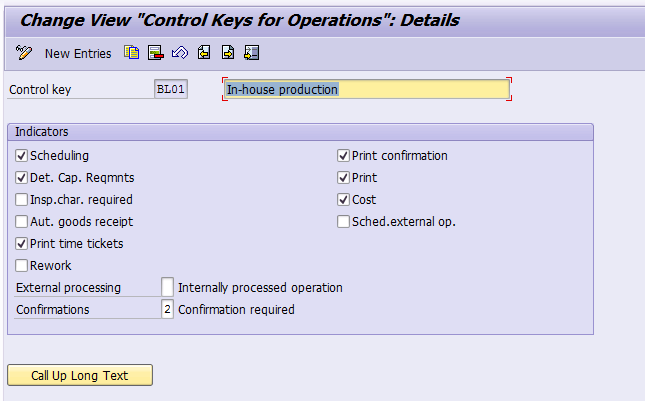
Availability Check Parameter (OPJK)
In SAP PP (Production Planning), the availability check parameter is a crucial aspect that governs how material availability is verified and managed during the production process. This parameter, also known as the availability check control, determines the rules and criteria used to check the availability of materials required for production orders or operations
- Material Availability Check: The availability check parameter defines when and how the system checks the availability of materials needed for production. It ensures that sufficient quantities of materials are available in stock or can be procured in time to fulfill production requirements.
- Scope of Check: The parameter specifies the scope of the availability check, including which types of materials are included (e.g., finished goods, components, semi-finished products) and which locations or storage locations are considered for checking availability.
- Checking Horizon: It defines the time horizon within which the availability check is performed. This horizon can extend from the current date to a future date based on the lead time for procurement or production of materials.
- Checking Rule: The availability check parameter determines the rule or logic used to evaluate material availability. This rule may consider factors such as safety stock, replenishment lead time, reservations, backorders, and special procurement types.
- Confirmation Control: In addition to checking material availability, the parameter may also control how production confirmations are processed and recorded. It specifies whether partial or final confirmations are allowed and how quantities and costs are updated based on confirmation data.
- Integration with Other Modules: The availability check parameter integrates with other SAP modules, such as Materials Management (MM) and Sales and Distribution (SD), to ensure consistency in inventory management, procurement, and order fulfillment processes.
- Alerts and Notifications: Depending on the configuration of the availability check parameter, the system may trigger alerts or notifications when material shortages or issues are identified. This allows planners and stakeholders to take timely corrective actions to prevent production delays or disruptions.
When you configure the Order availability checks at the point of Order creation or Order
release the following controls are available:

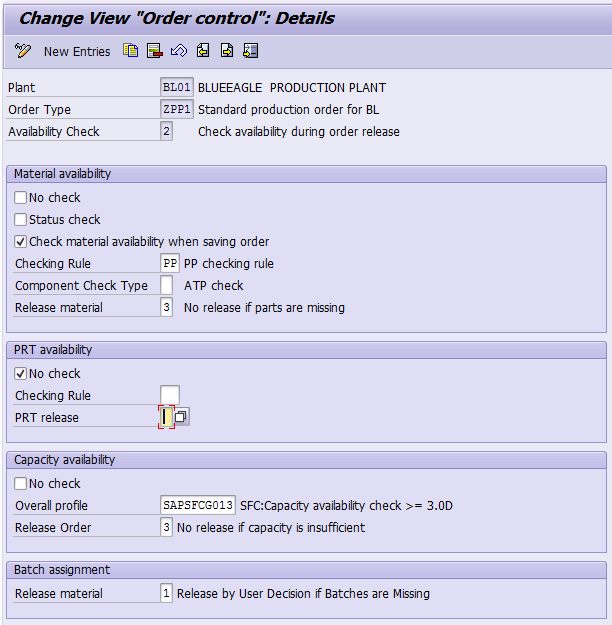


Define Confirmation Parameters
Confirmations parameters are to be set for orders types so as to allow confirmations as per the
client’s requirements.
Confirmations in SAP PP refer to booking the completion of production quantities at each
operation (partial completion or final completion). Confirmation is not receiving goods in
stock; it is only about declaration production at each operation and in turn booking cost
incurred in operational activities (in the background).
The method or manner in which these confirmations would happen is configured here.
In SAP PP (Production Planning), confirmation parameters refer to the settings and criteria used to control the confirmation process for production orders or operations. Confirmations play a vital role in updating the status and progress of production activities, as well as recording actual quantities, times, and costs incurred during production. Here’s an overview of confirmation parameters in SAP PP:
- Confirmation Control Key: The confirmation control key is a key element in defining confirmation parameters. It determines how confirmations are processed and recorded for production orders or operations. Each confirmation control key is associated with specific settings that govern the confirmation process.
- Confirmation Type: SAP PP supports various confirmation types, such as partial confirmation, final confirmation, and technical completion. The confirmation type determines the nature and purpose of the confirmation, such as indicating progress, recording actual production quantities, or confirming the completion of an operation or order.
- Confirmation Quantity: This parameter specifies whether the confirmation quantity can exceed the planned quantity for an operation or order. It allows flexibility in recording actual production quantities, accommodating situations where more or less material is used than initially planned.
- Confirmation Time: The confirmation parameters include settings for recording the start and finish times of operations. These settings define whether the system should automatically derive the confirmation times based on predefined rules or allow manual entry by users.
- Confirmation Status: Confirmation parameters control the status flow of production orders or operations based on confirmation activities. They determine how the status of an order or operation is updated when confirmations are recorded, such as changing from “planned” to “partially confirmed” or “fully confirmed.”
- Confirmation Costing: SAP PP enables the integration of confirmation parameters with cost accounting processes. Confirmation parameters define how actual costs, such as labor costs, machine costs, and overhead costs, are calculated and allocated to production orders or operations based on confirmation data.
- Confirmation Messages and Outputs: Confirmation parameters include settings for generating messages, notifications, and reports related to confirmation activities. These settings determine when and how users are notified of confirmation requirements, errors, or discrepancies.
- Confirmation User Exits and Enhancements: SAP PP allows for customization of confirmation parameters through user exits and enhancements. These tools enable organizations to extend standard confirmation functionality to meet specific business requirements or integrate with external systems.
Transaction Code: OPK4
Menu Path: Production -> Operations-> Confirmation -> Define Confirmation Parameters
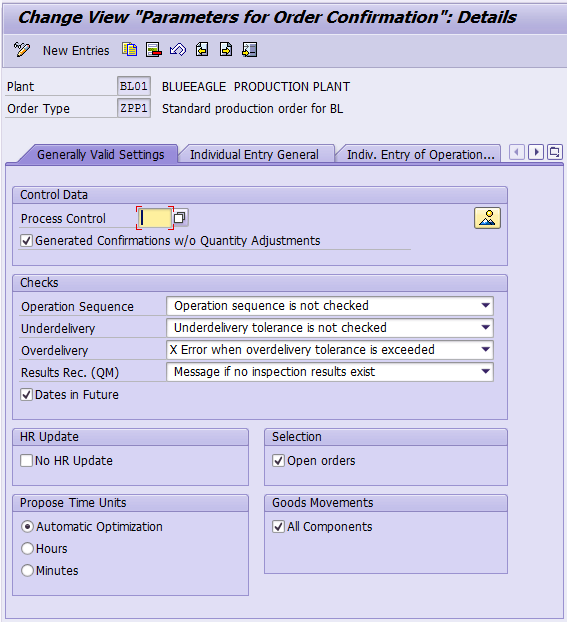
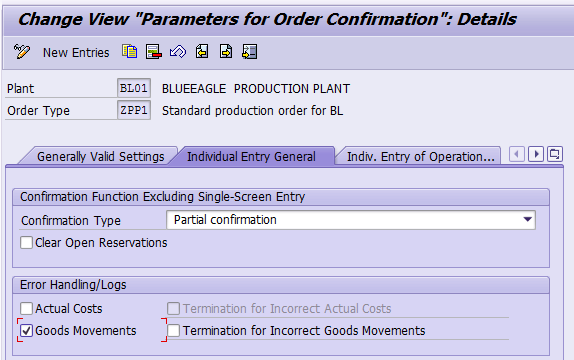

2 thoughts on “Control key in SAP PP”