Hello friends if you are looking for Define Storage location MRP per Plant in SAP PP | Planning File Entries in SAP Production Planning | Define Storage location MRP per Plant in SAP PP
Planning encompasses a set of processes and activities aimed at efficiently managing and optimizing production operations to meet customer demand while minimizing costs and maximizing resource utilization. SAP PP offers various functionalities and tools to support different aspects of planning within the production environment. Here’s an overview of planning in SAP PP:
Demand Planning: Demand planning involves forecasting customer demand for finished products based on historical sales data, market trends, and other relevant factors. In SAP PP, demand planning can be performed using tools such as Material Requirements Planning (MRP), Demand Management, and Sales and Operations Planning (S&OP).
Master Production Scheduling (MPS): MPS involves creating a detailed production schedule for finished products over a specified planning horizon. It considers factors such as production capacity, material availability, and demand forecasts to establish a feasible production plan. SAP PP supports MPS through functionalities such as Production Planning Strategies and Planning Time Fence.
Material Requirements Planning (MRP): MRP is a core component of production planning that calculates the materials needed for production based on the production schedule, bill of materials (BOM), and inventory levels. SAP PP includes MRP functionalities for generating procurement proposals, managing material reservations, and optimizing inventory levels.
Capacity Planning: Capacity planning involves assessing the capacity of production resources, such as work centers, machines, and personnel, to determine their ability to meet production requirements. SAP PP offers capacity planning tools to analyze resource capacities, identify bottlenecks, and optimize production schedules based on available capacity.
Production Orders: Production orders are used to execute manufacturing operations according to the production plan. SAP PP allows users to create, release, and manage production orders, assign resources, and track progress throughout the production process. Production orders can be generated automatically based on planned orders or manually created as needed.
Long-Term Planning (LTP): LTP involves strategic planning for production over an extended period, typically six months to several years. SAP PP supports LTP through functionalities such as Long-Term Planning Scenarios, Rough-Cut Capacity Planning (RCCP), and Material Forecasting.
Shop Floor Control: Shop floor control involves managing and monitoring production activities on the shop floor to ensure adherence to schedules, quality standards, and safety regulations. SAP PP provides tools for shop floor control, including Production Orders, Work Centers, Routing, and Confirmation functionalities.
Integrated Planning Processes: SAP PP integrates with other SAP modules such as Materials Management (MM), Sales and Distribution (SD), and Finance and Controlling (FICO) to support end-to-end planning processes. Integrated planning allows for seamless data exchange, real-time visibility, and coordinated decision-making across different functional areas.
Define Storage location MRP per Plant in SAP PP
Transaction Code: SPRO
Menu Path: Production → Material Requirements Planning → Planning Define Storage Location
MRP per Plant
a storage location is a physical or logical location within a company’s warehouse or plant where materials are stored, managed, and tracked. Storage locations play a critical role in inventory management, as they provide a structured framework for organizing and controlling the movement of materials throughout the production process. Here’s a detailed explanation of storage locations in SAP PP:
- Physical and Logical Locations: A storage location can represent a physical area, such as a warehouse, stockroom, or bin, where materials are physically stored. It can also represent a logical grouping of materials based on characteristics such as material type, storage conditions, or usage.
- Inventory Management: Storage locations serve as the primary unit of inventory management in SAP PP. Materials are assigned to specific storage locations within the SAP system, allowing for accurate tracking of stock levels, movements, and transactions.
- Material Movements: Materials can be moved between storage locations within the SAP system through various transactions, such as goods receipt, goods issue, transfer posting, and stock transfer. These movements are recorded and tracked in real-time, providing visibility into material flow and inventory status.
- Stock Placement: Storage locations define the physical arrangement of materials within the warehouse or plant. They determine where materials are stored, how they are organized, and how they can be accessed for production or distribution purposes.
- Storage Conditions: Storage locations can be configured with specific attributes and characteristics to accommodate different types of materials and storage requirements. This includes parameters such as temperature, humidity, shelf life, and hazardous material handling instructions.
- Batch Management: Storage locations are closely linked to batch management in SAP PP, especially for materials with batch-specific characteristics or requirements. Batch-managed materials are assigned to specific storage locations to ensure traceability and compliance with regulatory standards.
- Storage Bin Management: In addition to storage locations, SAP PP also supports storage bin management, which involves subdividing storage locations into smaller units or bins for more granular control over material placement and retrieval. Storage bins can be assigned specific attributes and capacities to optimize space utilization and streamline picking and replenishment processes.
- Integration with Other Modules: Storage locations in SAP PP are closely integrated with other SAP modules such as Materials Management (MM), Sales and Distribution (SD), and Production Planning (PP). This integration ensures seamless data exchange and consistency in inventory management processes across different functional areas.
Here we can define the default values for storage location MRP. The indicator that one set
here is proposed when creating a material master record for the storage locations maintained.
One has the following options for storage location MRP:
- Plan storage location separately
- Exclude storage location from MRP
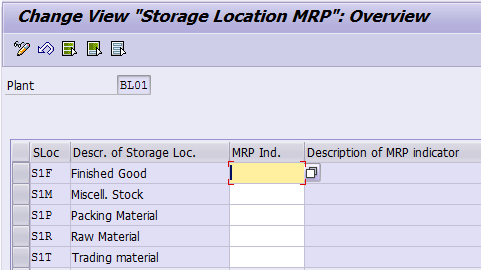
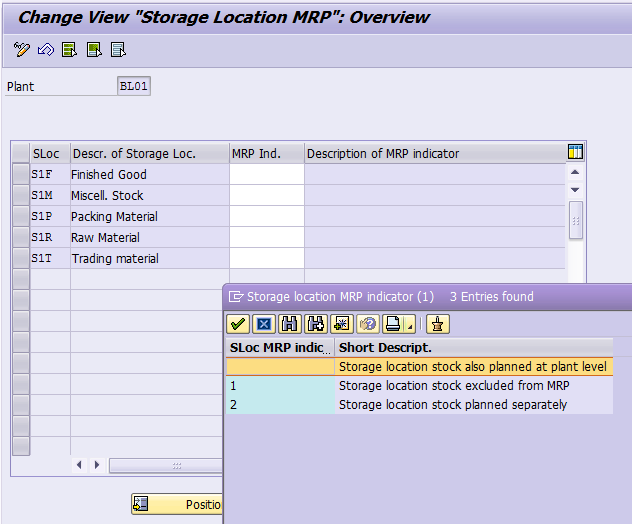
Planning File Entries in SAP PP
Activate MRP & Set Up Planning File
Transaction Code: OMDU
Activating MRP for the plant allows one to use the SAP MRP tool for the plant.
Menu Path: Production → Material Requirements Planning → Planning File Entries -> Activate MRP
& Set Up Planning File
Activate Material Requirements Planning
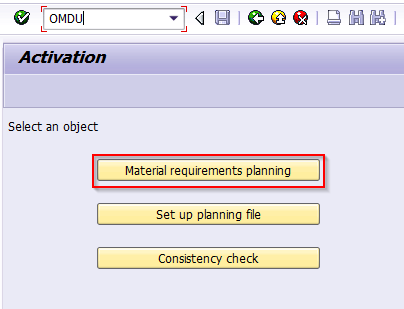
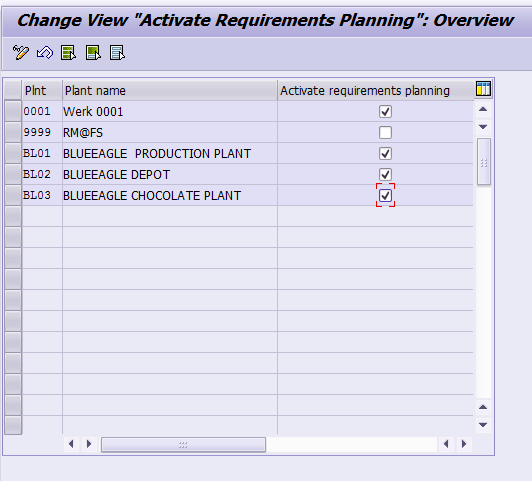
3 thoughts on “Planning in SAP PP”